Recently, as the global energy saving and consumption reduction prevail, the awareness of environmental protection has been continuously strengthened, and energy saving and emission reduction are the main direction of global industrial development. On the one hand, it is necessary to continue to develop energy-saving and emission-reduction technologies for internal combustion engines, and on the other hand, it is essential to develop new energy vehicles. The new EV is developing rapidly. It is a hybrid vehicle mainly driven by a motor and supplemented by gasoline or diesel. The sensors used in it mainly include sensors for detecting battery temperature, temperature sensors for monitoring motor temperature, and temperature sensor for battery cooling system, etc.
The basic component of a new EV is an electric motor (commonly known as a motor). To ensure motor’s life and optimal performance, the electric motor temperature also needs to be continuously detected, so it can work as accurately as possible within a temperature range of 140°C. Therefore, it is also crucial to determine the motor stator winding temperature, which allows the motor to take full advantage without risking overheating. In order to measure the temperature of the motor stator, the NTC temperature sensor in the motor needs to be easy to install, to ensure that it is free from mechanical stress during installation and operation, and has high dielectric strength to prevent arcing between the drive current circuit and the measurement current circuit. .
As the core component, the NTC chip is in electric motors in the form of double-layer packaged NTC temperature sensors, and plays an essential role in converting temperature variables into required electronic signals in the circuit. In the continuous high temperature environment of electric motors, NTC temperature sensors are required to respond quickly, which is a new requirement for NTC thermistors: high reliability (superior thermal shock performance), small thermal time constant (fast response).
As the picture following, the schematic diagram of NTC thermistor for electric vehicle motor includes chip 1 and electrodes. The chip is encapsulated with axial glass, and the electrodes are riveted after being bent.
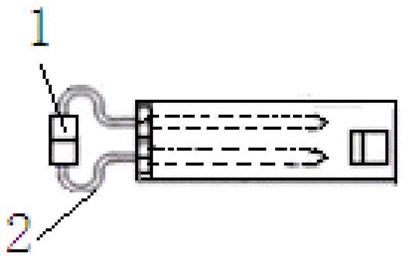
Disadvantages of NTC thermistor above for EV motor are as following:
(1) During the assembling and installation, the NTC thermistor is easily influenced by external mechanical stress, and lead to micro-cracks in the NTC thermistor chip. Meanwhile, the temperature-sensing glass bead is easily broken by external mechanical pressure.
(2) The exposed part of the lead wire is easy to contact with the coil in the stator winding of the motor, resulting in arcing, and is also easily affected by external corrosive gases, shortening its working life.
EXSENSE develops an NTC temperature sensor for EV motors, which can work in a high temperature environment. Under the premise of ensuring the mechanical strength of the NTC temperature sensor, it can achieve fast thermal response of NTC, excellent thermal shock performance, and high reliability, and small size.
How to make NTC Thermistor for EV Motors :
(1) Make an NTC thermistor: make a radial glass-encapsulated NTC thermistor, and cut the electrode 2 to about 3-4mm, as shown in the picture;
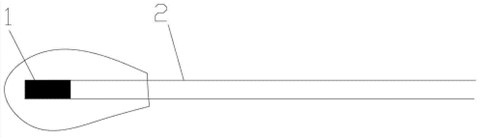
(2) Processing Lead wire 3: strip the two ends of the four-layer Teflon sheathed wire with braided mesh, and the length of the exposed conductors 32 is about 3mm, and the middle part is ringed in two sections with the outer Teflon sheath. The girdling section 31 by stripping is 20 mm, as shown in the picture;
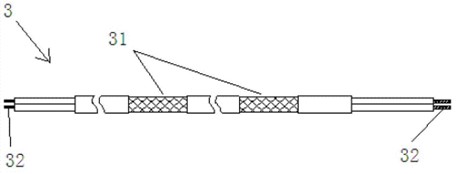
(3) Riveting: riveting the radial glass-encapsulated NTC thermistor and the conductors;
(4) Coating for the 1st time: coating the soldering point and the exposed part of the electrode by epoxy, and then cure, this part is insulated.
(5) Coating for the 2nd time: coating the front-end chip and leads again, then cure, and test its insulation performance after curing;
(6) Potting: pot the NTC thermistor after the second coating in the copper housing with high thermal conductivity and high temperature resistance epoxy. The copper housing has a constriction, which can stand greater cold and heat shocks and prevent the housing from falling off.